The Car
Thermec Zed Chassis
The final car will utilize Thermec Zed, a high performance 3D filament provided by Filo Alfa, as the material for the chassis construction. Thermec Zed has a high strength to weight ratio and is easily printed, making it the ideal material.
Active Suspension System
The car used in the nationals competition had solid front and rear axles, which hindered the car in several obstacles such as the articulation test and pipe bridge. The new suspension system is independent, which prevents body roll during these obstacles. Also, servos on the car change the tension of the shocks depending on the tilt of the car, preventing the car from flipping.
Machined Aluminum Differential Gears
The differentials are designed to be machined in-house, with all metal components. They are open differentials designed for minimum width in order to allow further A-arm length. The final gear reduction of 1:3 helps to increase torque in the powertrain, enabling the car to ascend steep inclines.
Silicone Cast Tires
The tires were cast in 3D printed molds using silicone rubber. Silicone material provides exceptional grip to slick metallic surfaces, which will be encountered throughout the course. Silicone I was used due to it's performance properties and environmentally friendly solvents. The tires use Closed Cell Foam to provide the desired flexibility, which is also a sustainable material.
Tow Hitch
The tow hitch is a 3D printed part designed to increase the car's mobility with a trailer attached. The tow hitch is lightweight yet durable, and can be easily retracted to save space when not in use.
Custom PCB
Because of the large amount of programming in the car, it is necessary to use custom circuit board to interface all of the sensors to the Raspberry Pi. The board was designed and tested in the lab before being sent to a company to be made professionally.
Body Shell
The body shell is modeled after a 1947 Dodge Power Wagon and protects all the electronics. The body is molded in kevlar infused carbon fiber for high strength and low weight.
The Software
Automatic Headlights
The car is equipped with automatic headlights. Data from a lux sensor mounted on top of the body shell is sent to the on board computer, a Raspberry Pi Zero. When the ambient light is below the specified lux reading, the headlights turn on. This is a required feature for the competition, and is tested on the track, when the car drives through a dark tunnel.
Tilt Warning System
Another competition requirement: the car has a tilt warning system that uses a buzzer or light to warn the driver when the car is tilted at an unsafe angle.
Telemetry System
Data recorded from the car's many sensors is live streamed to any device connected to the same network. Data such as the car's pitch, roll, and ambient light can be accessed from any computer, and from android phones with the telemetry app. In addition, telemetry data can be seen live with the team's Microsoft HoloLens. A rendered 3D image of the car moves with the car's orientation in real time.
Parallel Parking
Our car is programmed to autonomously parallel park. This means that at the press of a button, the car drives itself and searches for a suitable parking space. When one is found, the car maneuvers itself into the space. This is not required for the challenge, but it contributes towards the innovation portion of the engineering presentation.
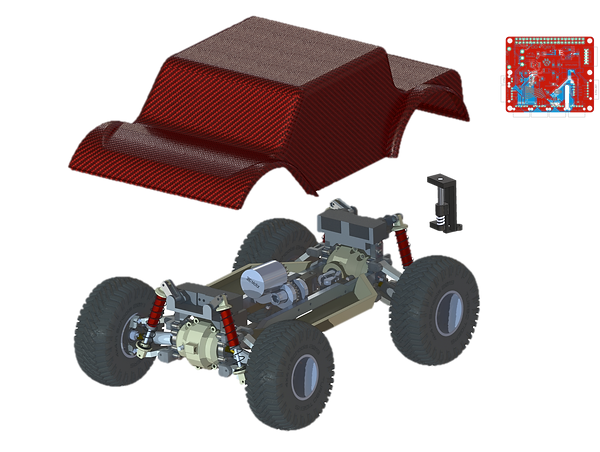